Revision as of 01:38, 22 May 2012 ddgonzal (Talk | contribs) (->Stage 3) <- Previous diff |
Revision as of 01:41, 22 May 2012 ddgonzal (Talk | contribs) Next diff -> |
||
Line 15: | Line 15: | ||
The big discussion: [http://datsun1200.com/modules/newbb/viewtopic.php?mode=viewtopic&topic_id=6428&forum=1 regarding Turbocharging A12]. Caution: difficult reading in that discussion. | The big discussion: [http://datsun1200.com/modules/newbb/viewtopic.php?mode=viewtopic&topic_id=6428&forum=1 regarding Turbocharging A12]. Caution: difficult reading in that discussion. | ||
+ | |||
+ | |||
+ | = Stage 1 = | ||
+ | 20% more HP than stock. | ||
+ | |||
+ | A stock A-series engine can take 10 psi. You don't even need an intercoolor, and so you can use draw-through on a stock carburetor. But blow-through is easier. | ||
+ | |||
+ | * Stock engine | ||
+ | * Loop piping from stock exhaust manifold | ||
+ | * Wrecking yard turbo ($100) | ||
+ | * Piping from turbo to stock carburetor top hat | ||
+ | * Set initial timing at 3 degrees | ||
+ | * Keep the stock vacuum advance (it will have no effect under boost) | ||
+ | * Fit larger power valve to carburetor | ||
+ | * Fit secondary main jet two sizes larger | ||
+ | |||
+ | Limit boost to 5 psi. | ||
+ | |||
+ | Or go to 10 psi for short bursts on cooler days. | ||
+ | |||
+ | = Stage 2 = | ||
+ | 1 bar (14.7 psi). 40% more HP. | ||
+ | |||
+ | * Use new Nissan rod bolts, torque to spec | ||
+ | * Use ARP head studs | ||
+ | * Fit Intercooler (precludes use of draw-through) | ||
+ | * Box the carburetor to go higher than 10 psi | ||
+ | * Rejet primary main two sizes larger. Secondary main 3 sizes larger. Power valve increase. | ||
+ | * Retard timing to 0 degrees. Connect vacuum advance up directly to manifold. This will help idle and starting out under low throttle, but the vacuum advance will have no effect under boost | ||
+ | * Use 75.5-degree [[thermostat]] | ||
+ | * Use custom exhaust manifold to mount the turbo | ||
+ | * 2" exhaust | ||
+ | |||
+ | = Stage 3 = | ||
+ | 100% more HP than stock. Requires modified engine, but not high-RPM usage. | ||
+ | |||
+ | 2 bar (28.2 psi) | ||
+ | |||
+ | Do all the stage 2 modifications plus: | ||
+ | * Custom pistons for low compression (7:1) | ||
+ | * A12GX head, ported | ||
+ | * EFI (or professionally modified & tuned box carburetor) | ||
+ | * custom inlet manifold with large runners | ||
+ | * 2.5" exhaust | ||
+ | * Spark retard system | ||
+ | * Water-injection system | ||
+ | * [[63-Series Transmission]] for A-series | ||
+ | * Heavy duty clutch | ||
+ | * H165 rear axle with traction bars | ||
= Supercharging vs. Turbocharging -- what's better? = | = Supercharging vs. Turbocharging -- what's better? = | ||
Line 189: | Line 238: | ||
[http://datsun1200.com/modules/myalbum/photo.php?lid=350 http://datsun1200.com/modules/myalbum/photos/thumbs/350.jpg] | [http://datsun1200.com/modules/myalbum/photo.php?lid=350 http://datsun1200.com/modules/myalbum/photos/thumbs/350.jpg] | ||
- | |||
- | = Stage 1 = | ||
- | 20% more HP than stock. | ||
- | |||
- | A stock A-series engine can take 10 psi. You don't even need an intercoolor, and so you can use draw-through on a stock carburetor. But blow-through is easier. | ||
- | |||
- | * Stock engine | ||
- | * Loop piping from stock exhaust manifold | ||
- | * Wrecking yard turbo ($100) | ||
- | * Piping from turbo to stock carburetor top hat | ||
- | * Set initial timing at 3 degrees | ||
- | * Keep the stock vacuum advance (it will have no effect under boost) | ||
- | * Fit larger power valve to carburetor | ||
- | * Fit secondary main jet two sizes larger | ||
- | |||
- | Limit boost to 5 psi. | ||
- | |||
- | Or go to 10 psi for short bursts on cooler days. | ||
- | |||
- | = Stage 2 = | ||
- | 1 bar (14.7 psi). 40% more HP. | ||
- | |||
- | * Use new Nissan rod bolts, torque to spec | ||
- | * Use ARP head studs | ||
- | * Fit Intercooler (precludes use of draw-through) | ||
- | * Box the carburetor to go higher than 10 psi | ||
- | * Rejet primary main two sizes larger. Secondary main 3 sizes larger. Power valve increase. | ||
- | * Retard timing to 0 degrees. Connect vacuum advance up directly to manifold. This will help idle and starting out under low throttle, but the vacuum advance will have no effect under boost | ||
- | * Use 75.5-degree [[thermostat]] | ||
- | * Use custom exhaust manifold to mount the turbo | ||
- | * 2" exhaust | ||
- | |||
- | = Stage 3 = | ||
- | 100% more HP than stock. Requires modified engine, but not high-RPM usage. | ||
- | |||
- | 2 bar (28.2 psi) | ||
- | |||
- | Do all the stage 2 modifications plus: | ||
- | * Custom pistons for low compression (7:1) | ||
- | * A12GX head, ported | ||
- | * EFI (or professionally modified & tuned box carburetor) | ||
- | * custom inlet manifold with large runners | ||
- | * 2.5" exhaust | ||
- | * Spark retard system | ||
- | * Water-injection system | ||
- | * [[63-Series Transmission]] for A-series | ||
- | * Heavy duty clutch | ||
- | * H165 rear axle with traction bars | ||
[[Category:Fuel System]] | [[Category:Fuel System]] |
Revision as of 01:41, 22 May 2012
Forced Induction comes in two forms: Supercharging and Turbo-supercharging. Both work well in a Datsun 1200!
Overview
discussion: s/charged a14
One thing to remember is that a method that works well isn't the only good way.
Wuote:
Forced induction.This is a subject that was vigorously & robustly debated in an extensive thread not so long ago, so have a play with the search function & you will likely find it.
Myself, & a few others prefered the ability of the positive displacement blower to deliver high levels of torque, almost instantly, at very low engine speeds, while a large number of others prefered the advantages that a turbo offers at higher engine speeds. The turbo debate was further broken down into blow through versus suck through.
See if you can find this thread & have a read through it all. With some luck ou will gain an insight of the advantaged & disadvantages offered by each system.
The big discussion: regarding Turbocharging A12. Caution: difficult reading in that discussion.
Stage 1
20% more HP than stock.
A stock A-series engine can take 10 psi. You don't even need an intercoolor, and so you can use draw-through on a stock carburetor. But blow-through is easier.
- Stock engine
- Loop piping from stock exhaust manifold
- Wrecking yard turbo ($100)
- Piping from turbo to stock carburetor top hat
- Set initial timing at 3 degrees
- Keep the stock vacuum advance (it will have no effect under boost)
- Fit larger power valve to carburetor
- Fit secondary main jet two sizes larger
Limit boost to 5 psi.
Or go to 10 psi for short bursts on cooler days.
Stage 2
1 bar (14.7 psi). 40% more HP.
- Use new Nissan rod bolts, torque to spec
- Use ARP head studs
- Fit Intercooler (precludes use of draw-through)
- Box the carburetor to go higher than 10 psi
- Rejet primary main two sizes larger. Secondary main 3 sizes larger. Power valve increase.
- Retard timing to 0 degrees. Connect vacuum advance up directly to manifold. This will help idle and starting out under low throttle, but the vacuum advance will have no effect under boost
- Use 75.5-degree thermostat
- Use custom exhaust manifold to mount the turbo
- 2" exhaust
Stage 3
100% more HP than stock. Requires modified engine, but not high-RPM usage.
2 bar (28.2 psi)
Do all the stage 2 modifications plus:
- Custom pistons for low compression (7:1)
- A12GX head, ported
- EFI (or professionally modified & tuned box carburetor)
- custom inlet manifold with large runners
- 2.5" exhaust
- Spark retard system
- Water-injection system
- 63-Series Transmission for A-series
- Heavy duty clutch
- H165 rear axle with traction bars
Supercharging vs. Turbocharging -- what's better?
Section under construction. Volunteers? You gotta present both sides.
B&M blown A14 (rootes-type supercharger)
B&M supercharged NAPS-Z engine (rootes-type blower)
Centrifugal supercharger (belt-driven turbine)
Compound Supercharging concept
Draw-through or blow-through turbo systems?
Section by datto_dave
The carburettor can be mounted in two positions on a turbo-charged engine, and a great deal of controversy exists as to which is better. The carburettor can me mounted such that it feeds air into the turbo then the turbo feeds it to the engine. This is known as a Draw-Through system.Under these conditions the carburettor operates more or less as it would on a naturally asperated engine. Another school of thought says that the carburettor should be mounted between the turbocharger and the intake manifold. This means that the turbocharger draws fresh air and pumps it into the carburettor, which then feeds the fuel/air mixture to the engine. This setup allows the use of an intercooler, which draw-through does not. In fact there are several advantages to a blow through over a draw through, because the fuel/air does not have to travel through the turbo. The blow through system requires a boost sensitive rising rate fuel pressure regulator in order to increase fuel pressure with boost pressure as the rpms rise.
Another snag to the blow-through system is that the carburettor must be enclosed in a pressure box and the fuel supplied to the carburettor must be at a suitable pressure above the boost pressure. This means the fuel pressure has to be regulated in accordance with the boost pressure at all times. My own personal preference to date has been for the draw-through system this is largely substantiated by other people in the industry who are running very high-powered turbocharged cars. Almost all are using draw-through systems. However, the speed equipment industry doesn’t stand still. A new development with blow through systems could change the picture. The specially designed for ‘blow-through turbo applications Dellorto side draught carburettors may well be that development.
Boxed-carb blow-through system
A third possibility exists; fuel injection. Here, the injection system has to be designed to measure the amount of air going into the turbocharger by whatever means. It then injects the correct quantity of fuel into the engine at whatever point is convenient. The butterflies for throttling the engine may be situated either prior or after the turbocharger, depending on ease of installation layout. If the injectors are situated in such a position that they injected into a high pressure boosted environment, then the injection pressure must be compensated for by whatever pressure the boost level has reached. Fortunately most fuel injection systems have ample fuel pressure to cope with as high as 40-45 psi used in alcohol burners.
Intercooler
An Intercooler is not needed. The first three years of the Porsche 911 Turbo didn't have one (75-77), yet this 3.0 liter turbo outperformed 7.5 liter NA cars. However there are very good reasons to use an intercooler, including:
- Intercooler is worth it as it significantly reduces the temperature of the compressed air, which increases the boost possible with a given octane fuel
- Using an aluminum radiator should be better than nothing. Unless someone actually tested this, we are all just guessing. Radiators can flow a lot of water, and air is easier to pump ... so air should flow through w/o significant restriction. Putting this in front of the car should allow some cooling effect, although obviously not as a much as a purpose-designed cooler.
- An alternative is to use water or alcohol injection. Some OEM applications used water injection (ex. 1962 Oldsmobile Jetfire)
Wastegate
A Wastegate is used for adjustable control over boost pressure. When the set pressure is exceeded, exhaust is routed around the turbine to go out the tailpipe
- Not needed if you carefully size the turbo to the application (ensuring that at maximum rpm, design boost is not exceeded). Older OEM applications used this method.
Blow-off valve (or recirculation valve)
A Blow-off valve is used to preventin the turbo from surging, for example during gear shift or whenever throttle is closed. Porsche uses these, so obviously they work.
- Blow-off intake boost to atmosphere. Boost is lost. Simple, inexpensive
- Blow-off to compressor inlet (recirculate back through turbo inlet). Used to enhance throttle response: Boost is kept in circuit for immediate availability when throttle is opened again
Carburetor Setup
- Injection is better, allowing better control of mixture
- Draw through was used by many OEM setups. It is reliable, and the simplest option. The downside is you can't use an intercooler, as the fuel will condense in the cooler.
- Blow through works well. The main reason to use this over a draw-through is so an intercooler can be used.
- Unboxed carb. This was a popular OEM method. phunkdotaspok says this can handle 10 psi with a good top-gasket seal. In an NA application, a warped top is not a problem, as there is no pressure in the float chamber. This only becomes important in boosted application.
- Need richer jets to keep air charge cool and prevent detonation
- * Boxing carb. This allows a more or less stock carb to be used, the outsided pressure balancing the inside pressure
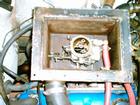
Fuel pump
- * Stock fuel pump is good for draw-through setup. It's not enough for a blow-through setup, as 2.5 boost would overpower the fuel pressure
- Using a low-pressure (15 psi) electric pump oughta be good for a 10-12.5 psi boost.
- Needle and seat has trouble holding more than 10 psi fuel pressure. Better to use a secondary 15-psi pump to cut in only when needed.
- Best setup is to use a rising-rate regulator with a high-psi pump. Excess fuel is returned to the tank.
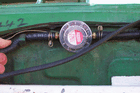
Turbochargers
- T3 is pretty big for an A12. Needs high rpm, head work, etc
- Mid-80s Nissan Pulsar turbo (E15 engine) has integral wastegate
- go_the_datto actually tried Daihatsu diesel 1.0 turbo on A12. Good response in lower rpm ranges. Two make better twin-turbo application for A12
Here is some helpful info on everything from how a turbo works to choosing the right turbo for your engine based on compressor maps Turbo Tech
Diesel vs. Petrol Turbos
Barpk: The main difference between a petrol and diesel turbo is its seals. Diesel turbos don't have positive seal turbo seals, which means that if put it in a suck-through system they can leak oil under extreme vacuum, which happens when throttle is closed. This is not a problem in a blow-through system.
Boost pressure
- 6-7 psi is what a lot of OEM applications use.
- 10 psi should be possible with a stock A12/A14
- 14.7 lbs gives theoretically double the airflow so max. power would be about 2x stock, but this isn't actually the result. The reason is that the stock induction and exhaust system won't flow this much air under pressure. However, the low rpm torque could approach 2x (at about 2250 rpm) if a small turbo is used. So a 130hp turbo engine will have much more performance than a 130hp NA engine
- 1986 Honda 1.5 liter ran boost of 4.0 bar - that's 300 bhp ... per cylinder with special fuel
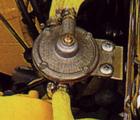
Induction and Exhaust
Obvious, for more airflow, a higher flowing carb, intake, heads (ports and valves) and exhaust system is beneficial.
Supercharging will increase power on a stock engine, but increasing the airflow capability of the engine will bring your blown engine to its full potential
This factory A14 forklift exhaust manifold might be useful:
Factory Turbo Systems
Might you spend less money and get more horsepower and reliability by swapping in a factory turbo moto?
Nissan Turbos
CA18DET
CA18DET Magazine article
Toyota 4A 1600cc engines
- A15 Specs from the article written by Davo1200 (http://datsun1200.com/modules/nsections/index.php?op=printpage&artid=13)
- 4A-FE Specs can be seen at redbook in a CS Seca for example (http://www.redbookasiapacific.com/au/vehicle/specs.php?key=TOYO90FZ)
- 4A-GE (wide angle DOHC) Come in 5 flavours ranging from 86kW (Gen 2) up to 121kW (Gen 5) 20 Valve.
- 4A-GZE supercharged. Some use this motor and its fuel system and computer for a turbo setup although simply replacing the cast pistons with forged items in a 4A-GE will yield the same result (except that an aftermarket ECU will be needed). The advantage over the supercharger is that boost can be variably controlled using and adjustable wastegate or boost controller. A supercharger has a fixed design boost, although aftermarket overdrive pulleys are available. They don't like to be spun more that around 8000 rpm as the teflon coatings on the roots can melt.
Datsun A15 | Toyota 4A-FE | Toyota 4A-GE (Gen 3) | Toyota 4A-GZE (AE101) | |
---|---|---|---|---|
Bore | 76 mm | 81 mm | 81 mm | 81 mm |
Stroke | 82 mm | 77 mm | 77 mm | 77 mm |
Displacement | 1488 cc | 1587 cc | 1587 cc | 1587 cc |
Power | 81 hp (60 kW) | 89 hp (66 kW) | 138 hp (103 kW) | 168 hp (125 kW) |
Although some have been able to extract more power from the 4A-FE. The upside is that they are very easily obtainable and so are parts. They are a narrow angle DOHC (single sprocket) cross-flow alloy head with a cast iron block.
Mazda Wankel Engine – Turbo
Mazda piston Engine – Turbo
references: regarding Turbocharging A12